Cobots producerer ventiler til brandslanger
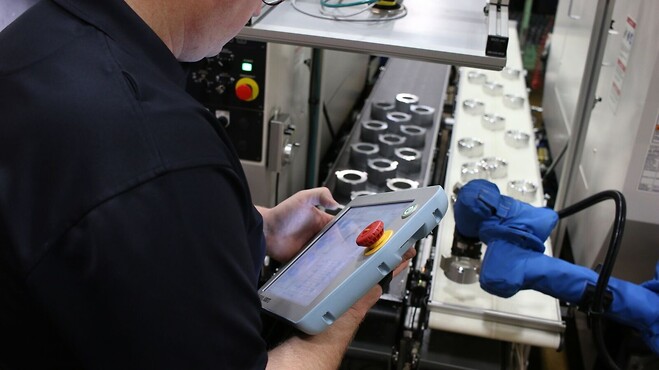
Task Force Tips i Indiana, USA, har integreret robotter med maskinværktøjer så langt tilbage som 1990. De robotter var dog dedikeret til udelukkende at arbejde på den maskine, de blev installeret med, og kunne ikke flyttes til andre maskiner:
Der sker så det, at maskinen slides op først, og så står man med en robot til 100.000 dollars, som man ikke kan bruge til noget. Vi havde hørt om samarbejdende robotter, som kunne bruges på en meget mere fleksibel måde, så vi besluttede at undersøge denne nye teknologi, fortæller Stewart McMillan, der er administrerende direktør hos Task Force Tips.
Virksomheden installerede én UR10-robot og to UR5-robotter til at passe CNC-maskinerne. En fjerde UR5 er monteret på et bord på hjul og flyttes fra opgave til opgave. Et scenarie, McMillan kalder “et fundamentalt paradigmeskift”:
- En væsentlig hindring for at bruge robotter førhen var den sikkerhedsafskærmning, der krævedes omkring maskinen. Det fantastiske ved UR-robotterne er, at man ikke behøver al den afskærmning. Vi kan rulle bordet med robotten helt op til maskinen og på et par minutter lære robotten at læsse dele.
Cory Mack, som er produktionstilsynsførende hos Task Force Tips, forklarer, hvordan UR-robotterne har reduceret personalebehovet fra syv til tre operatører:
- Nu tager det kun omkring en time per operatør per skift at betjene robotten, hvilket omfatter udlægning af dele og opsætning af robotten. Det betyder, at robotten kører i 21 timer uden overvågning, så vi opnår en besparelse på omkring 34 dage til at betale for robotten.
Reducerer nedetid
At have de to UR5-robotter til at arbejde sammen har også hjulpet med til at optimere produktionen. Når råemnerne ankommer på et indgående transportbånd, bruger den første UR5-robot visionsstyring til at identificere og samle råemnerne op og indføre dem i den første fræsemaskine.
Den ene UR5-robot tager derefter den halvt maskinbearbejdede del, som allerede er i drejebænken, og giver den til den anden UR5-robot. Den anden robot indsætter derefter delen i den anden maskine, tager den fuldstændigt maskinbearbejdede del ud og placerer den på det udadgående transportbånd, hvor en operatør placerer delene på anodiseringsstativer og afslutter cyklussen.
- Når vores medarbejdere ikke bruger tid på at holde en maskine kørende hele tiden, har de meget mere tid til at inspicere de bearbejdede produkter visuelt. Delenes kvalitet har nået et helt andet niveau med UR-robotten, og vores personale har fået mulighed for at komme med nye ideer og bedre metoder til at forbedre vores produktion, fortæller TFT’s produktionstilsynsførende, Cory Mack.